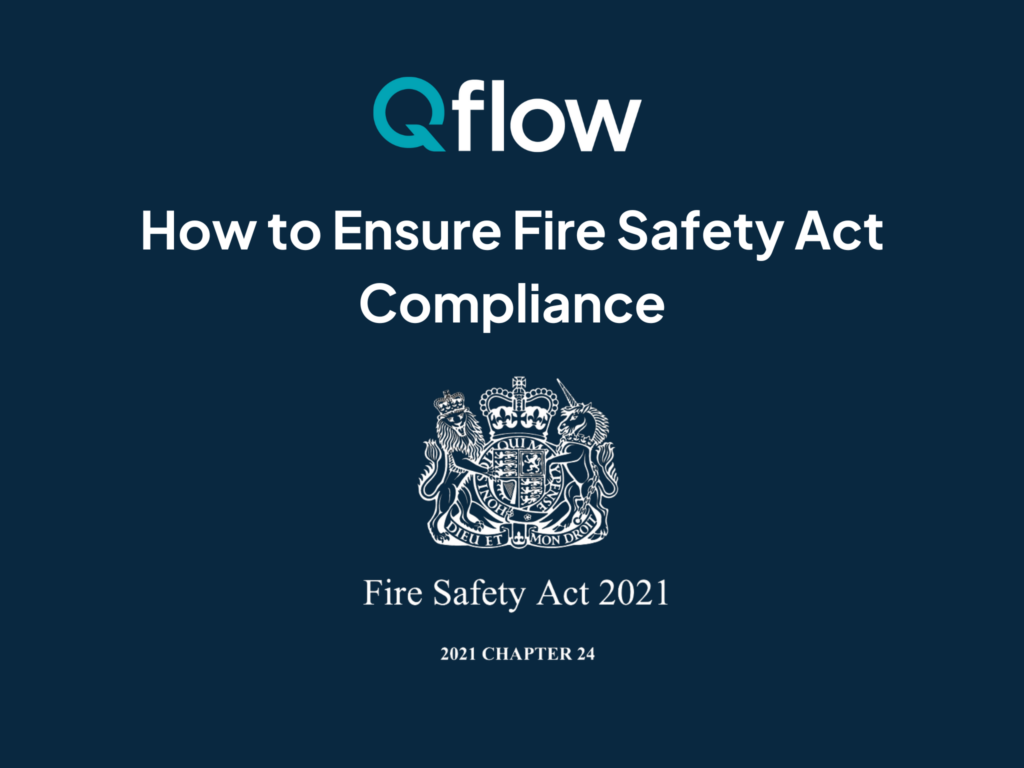
Since the tragic events of the Grenfell Tower fire in 2017, the Fire Safety Act 2021 (The Act) puts more onus on the construction industry to build residential buildings that are fire-safety compliant.
Inevitably, greater compliance responsibility creates a higher workload. For example, the need to carry out fire risk assessments at every stage of a building project, from design to completion. But as construction teams shoulder this responsibility while simultaneously working towards broader sustainability goals, how do they stay ahead, improve reporting accuracy and enhance site safety?
This article outlines your responsibilities per The Act and explains how to manage compliance, safety and sustainability in real time.
What is the Fire Safety Act 2021?
The Act, a UK law introduced in response to the 2017 Grenfell Tower Fire, aims to improve safety regulations for residential buildings, particularly high-rise buildings. The Act clarifies and strengthens England and Wales’s existing fire safety frameworks by amending the Regulatory Reform (Fire Safety) Order 2005.
Ultimately, The Act ensures greater accountability and transparency in managing fire risks by giving people responsible for multi-occupancy residential buildings a clear understanding of their duties and responsibilities under fire safety legislation.
So, what are my responsibilities under The Act?
Constructors, owners and managers of multi-occupancy residential buildings (Responsible Persons) are legally obliged to assess and manage risk in these areas:
- The structure and external walls of the building, including cladding, balconies, windows and doors
- The doors between individual flats and communal areas
What are the consequences of not complying with The Act?
Legal challenges around non-compliance or negligence have become more common due to the heightened focus on fire safety. Proven non-compliance with The Act can lead to unlimited fines, reputational damage, the loss of licenses or contracts, bankruptcy or even criminal charges and imprisonment. Non-compliance is not worth the risk, but at the same time, it’s a lot to manage.
3 common challenges when managing fire safety on construction sites
These challenges commonly get in the way of fire-safety compliance on construction sites:
- Precise assessments
Assessing a broader range of materials and structural elements for fire risk means tracking and managing more data. A manual approach to documenting fire risks, material management and safety protocols often leads to human error.
- Accurate reporting
Accurately documenting and communicating fire safety risks to relevant stakeholders is crucial and should also be consistent, comprehensive and clearly communicated. A lack of real-time data on compliance risks delays, risks of non-compliance and potential legal repercussions.
- Comprehensive monitoring and maintenance
Ongoing monitoring ensures fire safety measures remain effective against reported risks. But alongside this, additional environmental concerns linked to safety, such as waste management, are often overlooked.
So, what’s the solution?
Qflow: a digital solution for managing compliance, site safety and sustainability in real time
Qflow automates data collection on materials, waste and environmental risks, reducing manual errors and improving reporting accuracy. It helps to ensure your materials meet fire safety standards and tracks them at the on-site delivery point.
On-site monitoring and reporting
With Qflow, you can digitally capture goods received notes (GRNs) and track materials as they enter the construction site to eliminate the risk of non-compliant materials being installed.
There’s no need to chase material data from your supply chain. It integrates with existing site apps to make life easier for your team, leading to efficiency gains as you quickly and efficiently map your digital record of materials delivered against invoices.
Automated documentation
Automatically capturing and storing a record of materials on site required for fire safety assessments and streamlining the auditing process is easy with Qflow.
You can check your deliveries against project-specific requirements via a simple photograph (it checks for supplier certifications, such as FSC for timber and ISO14001 for suppliers for timber, and the 9 Duty of Care points required by the Environment Agency for waste). This simple ‘smart capture’ process saved 180 hours and 265 kg CO2e/m2 for Wilmott Dixon and FORE,
This automated data collection process reduces the risk of missing information or unchecked errors and keeps communication flowing with your supply chain. For KPI reporting, you can export the details recorded by the Qflow system into spreadsheets or PowerBI software.
Sustainability and Safety
With Qflow, you can track the entire material lifecycle, including waste management and disposal, a critical element in site safety and compliance.
It notifies your supply chain of non-compliant materials on site, helping them stay on top of waste management. For BW: Workplace Experts, Qflow: ‘revolutionised sustainability achievements in their London office fit-out project, streamlining processes and driving remarkable waste reduction’. Using Qflow, the BW team reduced site waste by 3.5 tonnes/100m2 waste intensity.
Conclusion
Introducing procedures that comply with The Act is necessary, but they must also be sustainable over time. Managing fire-risk compliance, safety and sustainability through an automated system is not only more straightforward, it’s also more accurate and comprehensive. Regulations will continue to change. The question is: are you prepared to adapt?
To find out more, get in touch.